Quality is essential for any business, affecting customer satisfaction, brand reputation, and ultimately their bottom line. However, attaining and sustaining quality comes with a price tag – the Cost of Quality (COQ). Uncovering these hidden costs associated with delivering superior quality is vital for businesses striving to be successful in their products or services while remaining profitable.
This article will explore COQ’s components, importance, and measurement techniques. We’ll delve into the depths of cost lurking beneath the surface and learn how businesses can accurately assess and manage them.
Additionally, we will look at how COQ contributes to continuous improvement and offer a bonus tip on utilizing time tracking for immediate insights into COQ. By the end, you will understand the importance of keeping tabs on the Cost of Quality to upgrade management practices and increase profitability.
Throughout this article, we’ll discuss:
- Understanding the Cost of Quality (COQ)
- COQ Components: Prevention, Appraisal, and Failure Costs
- Why Measure the Cost of Quality?
- How to Measure the Cost of Quality?
- Track Time to Measure COQ and Get Insights in Real Time
- Wrap-up: Keep an Eye on the Cost of Quality for Better Management and Profitability
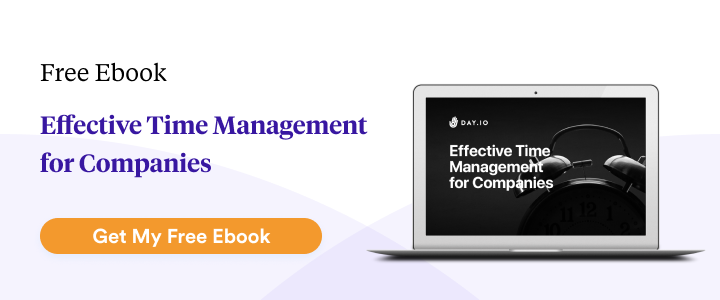
Understanding the Cost of Quality (COQ)
To understand the Cost of Quality, let’s first define what it is. COQ refers to all costs incurred in pursuing quality assurance and control. This includes costs associated with prevention, appraisal, and failure (which we will discuss later). The primary objective of measuring COQ is to improve an organization’s overall performance through quality improvement initiatives.
Here we’ll illustrate this with an example. A software development company is launching a new app for their customers. The company spends time and money for various purposes:
- Bug testing
- Code review
- User feedback
- Documentation
- Training team members
These activities aim to ensure the app is high quality and meets customer requirements. All these efforts result in an additional cost – the Cost of Quality. COQ is about money, time, and resources to ensure product or service delivery excellence.
COQ Components: Prevention, Appraisal, and Failure Costs
The Cost of Quality (COQ) consists of three essential components: prevention, appraisal, and failure costs. Understanding these components is crucial for businesses seeking to measure and manage quality-related expenses effectively. Let’s explore each element in detail:
Prevention Costs
Prevention costs are investments made upfront to prevent quality issues from arising in the first place. These costs focus on building a robust foundation for quality by implementing processes, systems, and training programs. By proactively addressing potential risks, businesses can minimize the likelihood of defects, errors, or failures.
Prevention costs can include activities such as:
- Employee training and education on quality standards and processes
- Designing and implementing quality management systems
- Conducting preventive maintenance on machinery and equipment
- Supplier evaluations and quality assurance programs
- Designing and implementing robust quality control measures
Appraisal Costs
Appraisal costs are incurred during evaluating and assessing products, services, or processes to ensure they meet defined quality standards. These costs involve activities to detect and address any non-conformities or deviations from desired specifications.
Examples of appraisal costs include:
- Inspection and testing of raw materials, components, or finished products
- Calibration and maintenance of measuring and testing equipment
- Quality audits and certifications
- Supplier quality assessments
- Costs associated with quality control personnel and their activities
Failure Costs
Failure costs refer to the expenses incurred when quality issues arise. These can range from customer service-related activities such as refunds, rework, and replacement of defective products to losses due to missed deadlines or reduced employee productivity.
We can further categorize failure costs into two types:
-
Internal Failure Costs
Internal failure costs occur when defects or quality issues are identified within the organization before the product or service reaches the customer. These costs include:
- Rework or repair non-conforming products
- Scrap or disposal of defective products
- Downtime or delays caused by quality-related issues
- Lost productivity and additional labor costs
-
External Failure Costs
On the other hand, external failure costs arise when customers or end-users identify quality issues after receiving the product or service. These costs include:
- Customer complaints and support services
- Product returns, replacements, or refunds
- Warranty claims and associated expenses
- Damage to the company’s reputation and potential loss of future business
Failure costs can be significantly higher than prevention and appraisal costs, making them a critical focus area for quality improvement efforts. Businesses can save resources and enhance customer satisfaction by reducing failure costs through effective prevention and appraisal activities.
Why Measure the Cost of Quality?
Measuring the Cost of Quality (COQ) is essential for businesses aiming to achieve sustainable success and maintain a competitive edge. Let’s explore the reasons why measuring COQ is crucial:
- Identify costly quality issues: COQ measurement helps businesses identify areas where quality issues occur and how much their efforts cost to rectify them. With the help of COQ, companies can focus on improving processes that are most prone to errors or defects.
- Allocate resources effectively: With accurate measurements, it is easier for organizations to make informed decisions about resource allocation and budgeting when achieving top-notch product or service quality.
- Greater visibility: COQ measurements provide organizations with a clear view of the quality performance of their products and services. This helps them identify areas where necessary improvement and adjust resources accordingly.
- Drive continuous improvement: With detailed insights into the cost of quality, businesses can make more effective decisions about process optimization and continual improvement initiatives.
- Ensure data-driven decision-making: Accurate measurement of COQ provides data that empowers business leaders to make informed decisions based on facts rather than guesswork or assumptions.
- Benchmark performance: The information obtained from measuring COQ helps companies measure their current performance against industry standards or competitors, enabling them to adapt and adjust their strategies accordingly.
- Enhance customer satisfaction: By taking a proactive approach to measure COQ, businesses can ensure that their products or services meet the highest quality standards, which leads to better customer experience and improved satisfaction levels.
How to Measure the Cost of Quality?
We can sum up the cost of quality under three main components: prevention, appraisal, and failure costs. So the COQ formula will be:
COQ = Prevention + Appraisal + Failure Costs
Here are seven key steps involved in measuring COQ across all components:
-
Identify Cost Categories
Begin by identifying and categorizing the various costs related to quality. Ensure that all relevant cost elements are included within each category to ensure comprehensive measurement.
-
Data Collection
This may involve reviewing financial records, invoices, payroll data, maintenance logs, customer complaints, and warranty claims. Use financial and operational data sources to ensure accuracy and completeness.
-
Quantify Costs
Allocate monetary values to each expense item within the identified categories. Financial records, invoices, labor hours and rates, and cost analysis concerning quality-related activities can all be used to determine these figures. Several standardized quantitative methods are available for you to maintain consistency and precision in cost quantification.
-
Calculate Total COQ
Sum up the costs within each category to calculate the total COQ. Add the prevention, appraisal, and failure costs (internal and external) to derive the comprehensive COQ figure.
-
Analyze And Interpret
Analyze the COQ data to gain insights into the cost drivers, trends, and patterns. Compare the COQ figures over time, across different products or services, or against industry benchmarks to identify areas for improvement and prioritize quality management efforts.
-
Continuous Monitoring
COQ measurement is not a one-time activity but an ongoing process. Implement systems and procedures to continuously collect, update, and analyze COQ data. Regularly review and monitor the COQ metrics to track progress, evaluate the effectiveness of quality improvement initiatives, and identify emerging quality-related issues.
-
Use Quality Management Tools
Finally, employ quality management tools and techniques to streamline COQ measurement. This may include using software applications or spreadsheets to capture and analyze data, conducting process mapping and value stream analysis to identify improvement opportunities, and employing statistical methods to quantify the impact of quality initiatives on cost reduction.
Track Time to Measure COQ and Get Insights in Real Time
Now that we’ve discussed several aspects of Cost of Quality (COQ) measurement let’s explore how time tracking can be a valuable asset. Accurate timekeeping gives organizations the data they need to accurately measure prevention, appraisal, and failure costs of COQ in real time.
Day.io is an excellent tool for doing just that – it’s a comprehensive time-tracking software designed to help streamline and optimize COQ measurement. Here are some of its noteworthy features:
- Time tracking with individual task and activity tracking
- Comprehensive project reports with cost breakdowns
- Cost and billing details to help with data-driven decision-making
- Overtime and paid time off calculation and approval
- Automated and manual timesheet approval
- Time and attendance monitoring
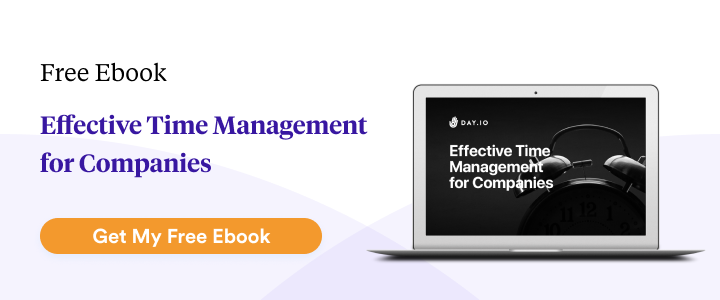
Wrap-up: Keep an Eye on the Cost of Quality for Better Management and Profitability
Measuring the Cost of Quality (COQ) is essential for businesses looking to achieve excellence in their products or services while preserving profitability. Organizations can gain invaluable insights into their quality management processes and make informed decisions to drive improvement by assessing and quantifying prevention, appraisal, and failure costs.
By keeping a watchful eye on the Cost of Quality, businesses can identify potential areas for improvement, allocate resources judiciously, and optimize their overall performance.
For efficient and effective COQ tracking that won’t break the bank, try automating your business’ time-tracking with Day.io. This easy-to-use solution will help you take control of your Quality Costs – quickly and accurately.